Video: Let’s Talk Smart Robotics: revolutionising industry 2025
Kanban è un sistema di pianificazione che viene utilizzato nei processi magri e nei programmi di rifornimento di inventario Just-In-Time per aiutare le aziende a migliorare la loro produzione e ridurre il loro inventario complessivo. Kanban è stato sviluppato da Toyota dopo la seconda guerra mondiale ("kanban" significa "cartello" o "cartellone" in giapponese) ma ha guadagnato un'ampia accezione in occidente fino agli anni '70.
Nei kanban tradizionali, i dipendenti utilizzano segnali visivi per indicare quanto deve essere eseguito durante un processo produttivo.
I segnali visivi consentono loro di sapere quando fermarsi o cambiare. Il processo sostituisce l'utilizzo previsto con l'uso effettivo in modo da contenere molto poco materiale in corso di lavorazione (WIP), riducendo così l'inventario.
Kanban è usato per ottenere l'efficienza - anche un concetto di Six Sigma. Il lavoro o il lavoro di produzione entra nel processo e procede attraverso di essa senza problemi e continuamente. Il processo riduce il WIP, riduce il lavoro e qualsiasi altro ritardo nel processo produttivo.
A causa della segnalazione visuale in tempo reale di Kanban, ogni area della linea di produzione estrae abbastanza componenti o materie prime e il giusto tipo di componenti che il processo richiede, al momento giusto.
Il grilletto per fare questo "tirare" è la carta kanban. Ciò può essere una scheda fisica o qualche tipo di segnale elettronico o altro segnale visivo (ho visto luci sui piani di produzione, come la luce blu speciale in un K-Mart). Per eliminare gli errori manuali e le carte perse, nel mondo di oggi molti (se non la maggior parte dei sistemi kanban che ho visto) sono elettronici.
I codici a barre vengono scansionati anziché l'uso di carte fisiche.
I due tipi più importanti di kanban sono:
Produzione (P) Kanban: Un P-kanban autorizza il centro di lavoro a produrre una quantità fissa di prodotto. La carta P-kanban viene trasportata sui contenitori associati.
Trasporto (T) Kanban: Un T-kanban autorizza il trasporto del contenitore completo alla stazione di lavoro a valle.
La tessera T-kanban viene trasportata anche sui contenitori associati al trasporto per passare nuovamente al ciclo.
Quando il contenitore sul pavimento di fabbrica è vuoto (perché le parti in esso sono state usate in un processo di fabbricazione), il contenitore vuoto e la sua carta kanban vengono restituiti al magazzino o al magazzino di fabbrica (il punto di controllo dell'inventario).
Il negozio di fabbrica sostituisce il contenitore vuoto sul piano di fabbrica con il contenitore completo del negozio di fabbrica, che contiene anche una scheda kanban.
Il negozio di fabbrica invia il contenitore vuoto con la sua carta kanban al fornitore (come ho detto, di solito elettronicamente in questi giorni).
Il contenitore completo del fornitore, con la sua carta kanban, viene consegnato al negozio di fabbrica; il fornitore mantiene il contenitore vuoto.
Questo è il passaggio finale del processo. Quindi, il processo non esaurisce mai del prodotto e potrebbe essere descritto come un ciclo chiuso, in quanto fornisce l'importo esatto richiesto, con solo un contenitore di ricambio, quindi non c'è mai eccesso di fornitura. Questo contenitore "di ricambio" consente l'incertezza nell'offerta, nell'uso e nel trasporto nel sistema di inventario.
Un buon sistema kanban calcola appena le carte kanban sufficienti per ogni prodotto.
Questa è la chiave per un efficiente sistema kanban - calcolo costante e re-calcolo dei formati bin bin kanban (numero di unità in ogni kanban) e anche numero di contenitori kanban.
Un esempio di una semplice implementazione del sistema Kanban è un "sistema a tre contenitori" per le parti in dotazione, dove non esiste una produzione interna. Uno scomparto è al piano di fabbrica (il punto di domanda iniziale), uno scomparto è nel magazzino di fabbrica o in un magazzino interno (il punto di controllo dell'inventario) e uno scomparto è presso il fornitore.
Quando il contenitore del kanban del pavimento della fabbrica si svuota, il sistema kanban invia un segnale al negozio di fabbrica o al magazzino interno per il rimontaggio kanban - che segnala al fornitore di fare lo stesso. In alcune operazioni ad alto volume, una dimensione kanban potrebbe essere una singola esecuzione di produzione, mentre il fornitore è tenuto a disporre di due o più contenitori kanban. Ciò accade anche se il fornitore ha un lungo tempo di consegna per la ricostituzione del bidone.
Le catene di approvvigionamento più ottimizzate hanno kanban nei processi principali.
Kanban necessita di un inventario accurato per essere efficace, in modo da integrare altri strumenti come il conteggio ciclo e gli inventari fisici.
20 Minuti al giorno per una catena di fornitura ottimizzata

Come ottimizzare la tua offerta di piccole aziende catena in soli 20 minuti al giorno. È possibile sapere cosa hai fatto ieri. Ecco come farlo.
Come la tua catena di fornitura sta cercando di uccidere la tua piccola Biz
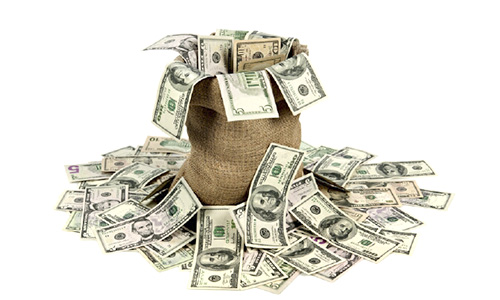
La catena è necessaria, non un male necessario. La tua catena di approvvigionamento ti costa denaro, succhia il tuo tempo e ti fa beffa. Ma ne hai bisogno.
Nessun dolore, nessuna catena - ottimizzazione catena di fornitura

Potrebbe non essere ottimizzata la catena di approvvigionamento. Farà male a fare i cambiamenti necessari per ottimizzare la vostra catena di approvvigionamento.